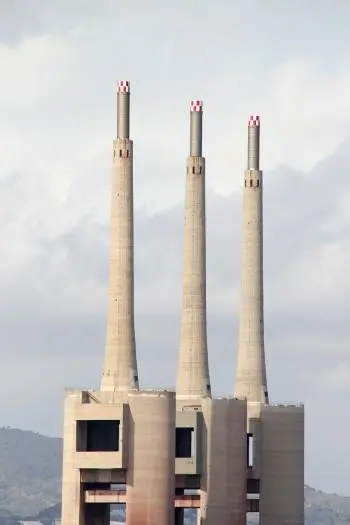
Une centrale thermique est une centrale électrique dans laquelle l'énergie thermique est convertie en énergie électrique. Dans la plupart des pays du monde, les turbines des centrales thermiques fonctionnent à la vapeur. L'eau est chauffée, se transforme en vapeur et fait tourner une turbine qui entraîne un alternateur. Après avoir traversé la turbine, la vapeur est condensée dans un condenseur et recyclée là où elle est chauffée ; c'est ce qu'on appelle un cycle de Rankine.
La variation la plus importante dans la conception des centrales thermiques est due aux différentes sources de chaleur : combustible fossile, énergie nucléaire ou énergie renouvelable. Les centrales électriques thermiques qui utilisent des énergies renouvelables sont principalement les centrales solaires thermiques et les centrales géothermiques.
Une centrale thermique est une centrale électrique qui convertit l'énergie thermique en énergie électrique. La différence entre un type de plante et un autre est la façon dont la chaleur est obtenue.
Fonctionnement d’une centrale thermique
Une centrale à vapeur fonctionne selon un cycle thermodynamique décrivant le processus par lequel l'énergie est extraite du combustible et convertie en électricité.
Dans une centrale thermique typique, le combustible (tel que le charbon ou le gaz naturel) est brûlé dans une chaudière pour produire de la chaleur. La chaleur est ensuite utilisée pour générer de la vapeur à haute pression dans une turbine à vapeur, qui entraîne un générateur électrique. Ensuite, l'électricité produite est fournie au réseau pour être distribuée aux consommateurs. Enfin, la vapeur qui en résulte passe dans une chaudière de récupération de chaleur pour redémarrer le cycle d'alimentation.
L'efficacité de la production d'énergie thermique d'un cycle de centrale à vapeur dépend de la différence de température entre le fluide de travail dans la chaudière et l'eau de refroidissement. Plus la différence de température est élevée, plus l'efficacité de l'alimentation est élevée.
La production d'électricité du cycle de ces centrales de production est la même quelle que soit la manière dont la chaleur est obtenue.
Composants d'une centrale à vapeur
Les principales parties d'une centrale à vapeur sont
-
Source de carburant : c'est la source d'énergie, et les carburants les plus populaires sont le charbon et le gaz naturel. Cependant, certaines stations utilisent une source d'énergie non conventionnelle, comme l'énergie solaire.
-
Chaudière : Dans la chaudière, le combustible est brûlé pour obtenir de l'énergie thermique et produire de la vapeur.
-
Turbine : le flux entraîne la turbine à vapeur pour obtenir de l'énergie mécanique.
-
Générateur : il est chargé de convertir l'énergie cinétique en énergie électrique.
-
Condenseur : il refroidit la vapeur pour obtenir à nouveau un fluide liquide et relance le cycle Vapeur.
Centrales à cycle combiné
Une centrale électrique à cycle combiné est une combinaison de centrale à gaz et une turbine à vapeur pour produire de l'électricité. Les deux turbines sont connectées à un générateur typique.
L'avantage d'une centrale électrique à cycle combiné par rapport aux autres types de centrales thermiques est qu'elle est plus efficace. Par exemple, l'efficacité d'une centrale électrique à cycle combiné peut atteindre 60 %, tandis que l'efficacité d'autres types de centrales thermiques n'est généralement que d'environ 30 %.
Cette efficacité accrue est due au fait que la chaleur résiduelle de la turbine à gaz peut être utilisée pour générer de la vapeur, que la turbine peut ensuite utiliser pour créer de l'électricité supplémentaire.
Le combustible pour ce type d'installation est le gaz naturel, le diesel et même le charbon s'il est préparé d'une manière particulière.
La principale caractéristique du cycle gazeux est que le fluide ne subit pas de changement de phase. Par conséquent, le processus est le suivant : compression du gaz, chauffage du gaz et enfin, détente du gaz dans une turbine à gaz. Dans ce cas, la turbine est reliée à un générateur électrique pour produire de l'électricité.
Le gaz qui sort de la turbine à gaz est encore à très haute température, il est donc utilisé pour générer de la vapeur et activer en parallèle un cycle vapeur classique.
Le cycle de Rankine
Le cycle de Rankine est le cycle de centrale à vapeur le plus courant. C'est un système en boucle fermée qui utilise l'eau pour créer de la vapeur et entraîne une turbine pour produire de l'électricité. Puis, enfin, la vapeur est refroidie et condensée en eau, pompée à nouveau dans la chaudière pour recommencer le cycle.
Le cycle de Rankine porte le nom de William John Macquorn Rankine, un ingénieur écossais qui l'a développé en 1859.
Le cycle de Rankine idéal est illustré dans les diagrammes pv et Ts ci-dessous. Il se compose de quatre processus :
-
1-2 : Faire bouillir de l'eau en vapeur à pression constante (processus isobare).
-
2-3 : Détente de la vapeur à travers une turbine à entropie constante (processus isentropique).
-
3-4 : Condensation de la vapeur à pression constante (procédé isobare).
-
4-1 : Repompage de l'eau dans la chaudière à entropie constante (processus isentropique).
Dans un cycle de Rankine réel, il y a des pertes de rendement dues aux irréversibilités (pertes par frottement dans la turbine et l'échangeur de chaleur, par exemple). Ceux-ci peuvent être minimisés en utilisant de la vapeur surchauffée et en la réchauffant avant qu'elle n'entre dans la turbine. Le réchauffage augmente également la puissance de sortie du cycle sans augmenter la consommation de vapeur.
Centrales à vapeur fonctionnant à l'énergie solaire
Les centrales solaires thermiques utilisent les rayons du soleil pour produire de la vapeur. En tant que centrale à vapeur ordinaire, la vapeur est utilisée pour faire tourner une turbine, qui alimente un générateur électrique.
Les centrales solaires thermiques peuvent être « à concentration » ou « sans concentration ». Dans une usine de concentration, des miroirs concentrent les rayons du soleil sur une petite surface, ce qui chauffe un fluide de travail qui la traverse.
Dans une usine sans concentration, les miroirs réfléchissent la lumière du soleil sur un grand récepteur rempli de fluide. La chaleur du soleil réchauffe ce fluide, qui fait alors tourner la turbine. Les centrales solaires thermiques sont généralement construites dans des zones sèches et ensoleillées.
La concentration d'énergie solaire à ce point génère des températures très élevées utilisées pour créer de la vapeur.
Désormais, le fonctionnement est le même que dans n'importe quelle centrale thermique classique.
En comparaison avec les centrales thermiques à flamme, telles que les centrales à charbon ou à gaz,c’est que le source d’énergie est inépuisable. Pour cette raison, la production électrique de ces centrales est renouvelable
Avantages d'une centrale thermique
Les avantages d'une centrale thermique sont multiples.
-
Ils sont relativement peu coûteux à construire et à exploiter.
-
Ils peuvent être construits rapidement, ce qui est essentiel dans les zones où il y a un besoin de nouvelles centrales mais pas assez de temps pour attendre la construction d'une centrale nucléaire.
-
Les centrales à cycle combiné au gaz naturel sont beaucoup plus efficaces (atteignant 60 %) que les centrales thermiques conventionnelles.
Inconvénients d'une centrale thermique
Les centrales thermiques ne sont cependant pas sans inconvénients.
-
Un inconvénient majeur est qu'ils sont l'une des principales causes de pollution de l'air en raison des émissions des cheminées. Ces émissions peuvent comprendre du dioxyde de soufre, des oxydes d'azote et des particules.
-
Les centrales thermiques sont également une source majeure d’émissions de gaz à effet de serre, principalement sous forme de dioxyde de carbone. Actuellement, les centrales avec turbines à combustion sont obligées de contrôler leurs émissions. Cette obligation est particulièrement pertinente pour les grandes centrales où il existe une section importante pour réduire les polluants.
-
Ils peuvent aussi polluer l'eau. Par exemple, les tours de refroidissement associées aux centrales thermiques utilisent de grandes quantités d'eau, qui peuvent être une source de pollution de l'eau si elles ne sont pas traitées correctement.
-
Les centrales électriques au charbon sont souvent situées dans des zones à forte demande en électricité mais avec un approvisionnement en eau limité. Cela peut mettre à rude épreuve les ressources en eau locales.